Inspection and production systems for the tire industry
Micro-Epsilon is a reliable partner for precise inspection, monitoring and automation in the tire industry.
From the development of sensors, systems and software to production, installation and comprehensive customer service - we offer end-to-end support worldwide. In addition, we can respond quickly and with high flexibility to your individual requirements.
From single sensors to complex high-tech machines: from temperature sensors to width and thickness measurement of rubber materials through to AI-based visual inspection systems along with tire uniformity and geometry lines:
Everything from a single source - all from Micro-Epsilon.
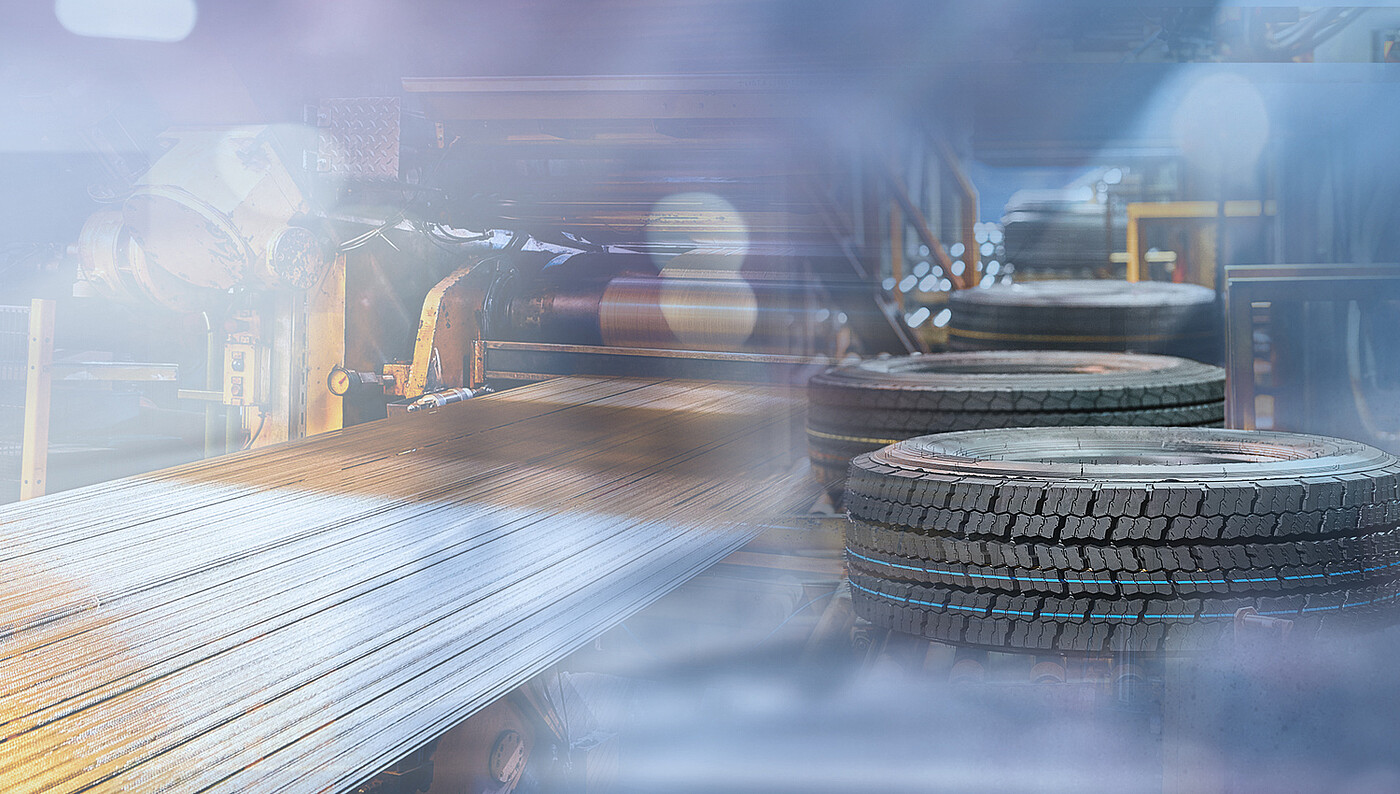
Reliable and long life solutions
One of Micro-Epsilon's strengths lies in the strong and long-standing cooperation with our business partners. With Micro-Epsilon, you can rely on a partner who will stand by your side in the long term.
Through reliability, openness, predictability and flexibility, we create the basis for a trustful partnership. This is how we ensure close cooperation based on mutual trust and reliability.
Are you looking for systems that offer maximum efficiency for your investment and maintenance budgets over a period of 3 or more years?
Then you are perfectly right at Micro-Epsilon!
The crucial point here is that with Micro-Epsilon products, you achieve the lowest cost per produced meter of tire component material or per tire - and therefore the best value for your investment. Just get in touch!
We optimize all cost factors:
- Purchase and installation of the machine
- Operating costs including energy consumption
- Costs for spare parts
- Service costs after the warranty period
We divide these total costs by the quantity of produced tire component material or the number of tires produced - so you know the exact value per meter or tire produced.